ガードに対する要求事項
ガードに対する一般的な要求事項としては、丈夫であること、ガードが原因で新たな危険源が生じないこと、バイパスや無効化が容易にできないこと、可能な限り生産工程の視界を妨げないことなどが重要です。
これら以外にも、ガードの種類に応じて以下のような要求があります。
1. 固定式ガードに対する要求事項
固定式ガードは、以下によって取り付けた位置に確実に保持されなければなりません。
●溶接などによって恒久的に固定される、または
●特殊ドライバなどの工具を使用しなければ外したり、開けたりできないように、ねじやナットを用いて固定すること。
2. 可動式ガードに対する要求事項
可動式ガードには、一般に次のような要求があり、必要に応じて機械の制御システムと連携しなければなりません。
●閉じているときはもちろん、開いているときもヒンジまたはガイドレールなどによって、機械類またはその構造物に固定されている状態であること。
●機械の可動部分にオペレータが到達可能な場合、機械の可動部分を起動できないこと。
また、機械の可動部分を起動した後、オペレータは到達できないようになっていること。この仕組みは可動式ガードのうち、インターロック付きガード(必要な場合はロック付き)を用いることで実施できます。
●可動式ガードのガードがズレたり外されたり、または取り付けたインターロック装置などが欠落あるいは故障したりした場合は、機械の可動部分の起動は防止されること。または機械が稼働していた場合、可動部分を停止させること。これは制御システムを自動監視することで実施できます。
3. 起動機能インターロック付きガード(制御式ガード)に対する要求事項
起動機能インターロック付きガードは、ガードを閉めると他の起動制御器(起動スイッチなど)を用いることなく自動的に機械の起動を行う、インターロック付きガードの特殊な形式です。このガードは、次のすべての要求を満足できる場合だけ実施してもよいとされています。
●基本的にインターロック付きガードとしてすべての要求事項を満足していること。
●機械のサイクルタイムが短い。
●ガードが開いている間の最大時間は、小さな値にセットすること。 (例:サイクルタイムと同等)
この時間を超えると、ガードが閉じても起動できないこと。この場合、リセット作業を必要とします。
●ガードが閉じたときには、必ず身体のすべてが危険区域から完全に外(安全位置)へ出るような機械の寸法または形状であること。
●起動機能付きインターロック付きガードに使用するインターロック装置は、故障によって意図しない起動などを生じないように、たとえば、二重化および自動監視するように設計されていること。
●ガードがそれ自体の重量によって下に降りている間に誤って起動を開始することがないように、たとえば、ばねまたはカウンタウエイトなどによって開いた状態を確実に維持できること。
4. エミッションの低減
本質的安全設計方策で十分に低減できなかった騒音、振動、危険物質(ガス・蒸気)などは、消音装置、振動減衰装置、該当区域の強制換気などの方法で保護方策を実施すること。
検知保護装置の選択と実施
物理的な遮蔽物であるガードとは別に、検知保護装置の種類と適用に関しても規定されています。用途に応じて適切な装置を選択する必要があります。
1)検知保護装置の種類
ライトカーテン(能動的光電保護装置:AOPD (注))
検出区域に存在する不透明な物体によって、遮光されたことを検出する光電子発光器と受光器とによって検知機能を行う装置。(ESPE(注)の1種、タイプ2と4があります。)
レーザスキャナ(拡散反射型能動的光電保護装置:AOPDDR(注))
その装置の光電式投光器が発生する放射光が、設定された二次元検出区域に存在する物体を照射して生じる拡散反射光を、光電受光器が検知することによって物体を検出する装置。(ESPEの1種、タイプ3があります。)

圧力検知マット
人がマットを踏むことにより、マットに作用する圧力の変化を感知(抵抗値の変化など)して、人体や物体の存在を検知する装置。
トリップバー、トリップワイヤ
上記の検知保護装置は、人体など不透明な物体の通過検出(トリップ)、安全防護領域内での存在検知、またはその両方の目的のために使用されます。
注)参考
・ESPE(electro-sensitive protective equipment):電気的検知保護装置
ライトカーテン、圧力検知マット、レーザスキャナなどを含み、保護トリップや存在検知を行う。
・AOPD(active opto-electronic protective device):能動的光電保護装置
一般にライトカーテンのこと。ESPEの1種。
・AOPDDR(active opto-electronic protective device to diffuse reflection):拡散反射形能動的光電保護装置
一般にレーザスキャナのこと。ESPEの1種。
2)検知保護装置の使用にあたっての留意事項
●検知保護装置を迂回して危険源に近づけることのないよう、適切な位置に取り付けること。
例えば、ライトカーテンの場合、上下・左右の隙間から光軸を迂回して危険源に手などを入れることができないようにします。
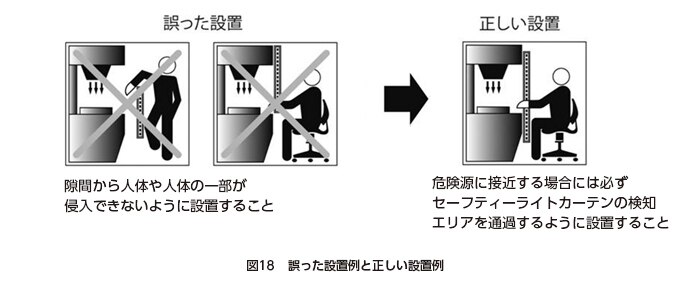
●人と危険源との間には、検知保護装置と機械の両方に必要な総合的な停止時間を考慮に入れて安全距離を設けること。
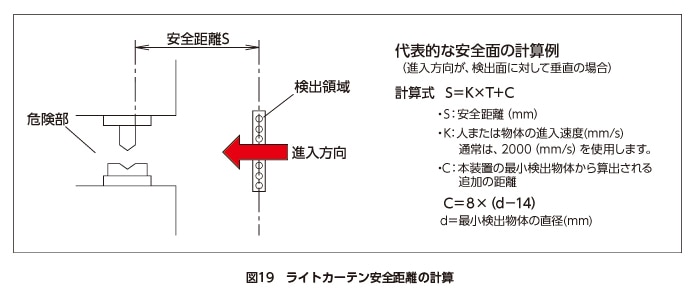
●検知保護装置は、人または身体の一部を検出すると、即座に停止命令を発すること。
●人または身体の一部が検知区域から退出したこと自体で、機械の危険源が再起動しないこと。また、検知保護装置の停止命令は、次の命令が出されるまでシステムとして維持されなければならない。
●再起動は、オペレータが危険区域の外に配置した制御装置(再起動用スイッチ)を、自分の意志で操作することによってのみ行われること。
●検出されることなく危険区域に入れたり、危険区域内に存在できたりすることを防止すること。このためには、必要に応じて固定式ガードなどと共に用いる場合があります。
なお、次の場合には検知保護装置だけでは不十分です。追加の保護方策や検知保護装置の使用自体の見直しが必要です。
●危険区域から、材料の切りくず、切削油などが飛び出してくる場合
●騒音、粉塵、X線などが放出される場合
●工程途中で不規則な長い停止時間があり、機械が完全に停止していると誤解されるような場合
●1サイクルの途中で緊急停止できないような特性を持っている場合(機械可動部の慣性力が大きい場合)
3)サイクル制御が自動で再開始するための検知保護設備の安全要求事項
主として生産性向上のために、人または人の一部が検知保護装置の検出区域から出ることで、自動的に機械のサイクル起動を再開することが例外的に認められています。ただし、様々な条件や要求事項があります。詳細はISO12100本文をご覧ください。
リスク低減を行った後でも、機械の意図する使用および合理的に予見可能な誤使用により、付加保護方策を必要とする場合があります。付加保護方策には、主に以下のような5つの代表例があります。
●切迫した非常事態を回避するために、人の意思で機械を即座に停止できるように、非常停止機能を備えること。
●機械に捕捉された人のための脱出手段、および脱出が不可能な場合の救助のための手段
●メンテナンス時などに備えて、動力(電力など)の完全遮断および内部に蓄積したエネルギをなくす方策
●機械を含む重量物の安全な取扱いに関する方策
●機械類の該当部分に安全に接近または出入りできる方策
非常停止機能
・非常停止用押ボタンスイッチなどのアクチュエータ(キノコ形の押しボタンなど)は、はっきりと解り、速やかに接近して操作できること。
・非常停止用押ボタンスイッチなどを押して非常停止指令が出されると、新たな危険源を生じることなく、可能な限り速やかに停止すること。
・非常停止指令は、リセットされるまで持続されること。(機械は停止した状態を保つ)
・非常停止指令のリセットは(非常停止用押ボタンスイッチのリセット)、その指令が出された位置でだけ可能であること。
・非常停止機能のリセットで機械は再起動してはならず、再起動の許可だけとしなければならない。
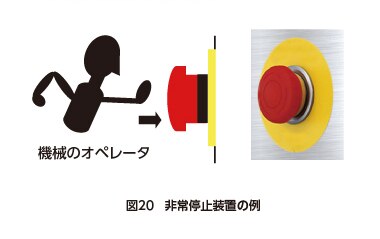
捕捉された人の脱出および救助のための方策
・外部への脱出ルートの確保。または一時的にでも安全に退避できる避難場所の確保。
・非常停止指令により機械が停止してから、特定要素を手で動かすための手段の確保。
・特定の要素を逆転させる方策
・安全に下へ降りる装置およびそのための係留具
・捕捉された人が救助を求めるための伝達手段
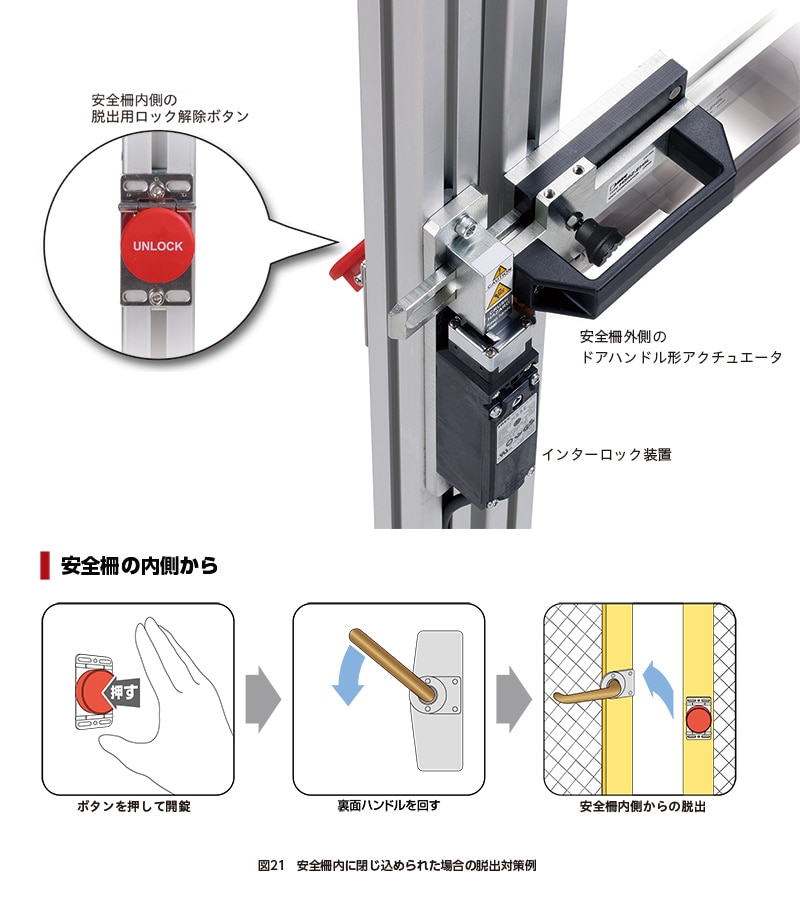
遮断およびエネルギの消散に関する方策
●機械(または該当部分)を動力供給から切断、分離できること。
●すべての遮断装置を“遮断”の位置において南京錠などで施錠できること。
●危険源を生じる蓄積エネルギをなくすか、それができない場合は封じ込めること。
重量構成部品の安全な取扱い
重い機械は、つり上げ装置による運搬に適切な装置を備えておくか、運搬用装置を安全に装着できること。
●スリング、フック、アイボルトまたは固定用のねじ穴を備えたつり上げ用具を備えること。
●フォークリフトで運搬される機械のための案内溝を備えること。
機械類への安全な接近
●すべての作業はできるだけ地上レベルで行えるように設計すること。これができない場合は、安全に接近できるプラットフォーム、階段などを設けなければならない。
●機械類の高所にある部位への接近手段は、墜落に対し保護手段を備えなければならない。(例:階段、はしご、およびはしごの安全囲い、墜落に対する係留具)
●歩行区域は滑らないような材質で製作すること。
●パネル表面に取り付けられたスイッチなどの制御装置が、足を掛けて踏み台にされるどの接近のための補助具として使用されることを防止するような設計・配置とすること。
本質的安全設計方策や安全防護を講じてもなお、残留するリスクに関しては、使用上の情報として機械の使用者に明確に伝える必要があります。
その際、運搬,組立及び設置,コミッショニング(立上げ,検収,引渡し,移管),設定(段取りなど),ティーチング若しくはプログラミング又は工程の切替え,運転,清掃,不具合(障害)の発見及び保全および必要ならば分解,使用停止,廃棄処分など、機械の運用に関係する各局面について伝える必要があります。
使用上の情報には、以下の内容が含まれます。
●機械の“意図する使用”について、安全で正しく機械を使用するための全ての情報。
●残留リスクについて通知や警告。また、訓練および保護具の必要性、追加のガードおよび保護装置の必要性があればそれらも述べること。
●意図しない使用や合理的に予見可能な誤使用に起因するリスクについての警告など。
信号および警報装置を使って危険事象の警告を行うこと
表示灯・点滅灯、またはブザー・サイレンなどを機械の状態を知らせる警告信号として使用します。ただし、これらの信号には次のことが必要です。
●危険事象が発生する前に発せられること。
●人がハッキリ認識できる信号であること。
また、これら警報装置は容易に点検できることが必要です。(点検に手間が掛かると、定期的な点検を怠る可能性があります。)
また、頻繁な発信による感覚飽和や警報装置の無効化を避けることに注意が必要です。
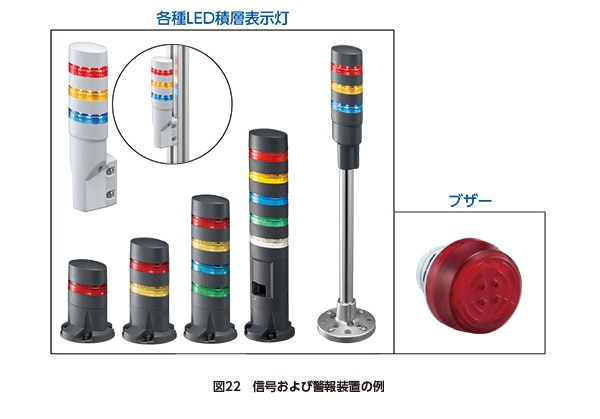
表示、警告文、マーク
・製造業者の名前、住所、製品のシリーズ名および製造番号(あれば)。
・要求事項への適合マーク(CE、ULマークなど)の表示。
・各種注意/警告マーク。(ただし、単に「危険」とだけ書くのではなく、何が危険なのかを表現すること)
・標識(絵文字)は警告文よりも素早く認識できるので、優先して用いることが望ましい
・警告文は,機械を使用する国の言語で最初に書き,要求があればオペレータが理解できる言語で書かなければならない。
付属文書(特に、取扱説明書)
1. 機械の運搬、取扱い、保管に関する情報
2. 機械の設置および立上げ、検収、引渡し、移管(コミッショニング)に関する情報
3. 機械自体に関する情報
4. 機械の使用に関する情報(意図する使用、合理的に予見可能な誤使用および禁止事項、使用すべき保護具、訓練など)
5. 保全に関する情報。たとえば、次を明確に区別して提示する。
・熟練要員(保全要員、専門要員)に限定して実行される保全作業に関する指示
・使用者(たとえば、オペレータ)によって実行してよい保全作業に関する指示
6. 分解、使用停止および廃棄処分に関する情報
7. 非常事態に関する情報(故障時の運転方法、消火設備など)
取扱説明書
取扱説明書の作成や表現については次を適用する。
1. 印字のフォントおよび大きさは最も明瞭に判読できなければならない。安全に関する警告および/または注意は,色彩,記号および/または大きな活字体を使用して強調しなければならない。
2. 使用上の情報は,機械が使用される国の言語で最初にかつ最初の版に記載しなければならない。複数の言語を使用する場合は,各々の言語は他の言語と容易に区別でき,翻訳文とこれに関連する説明図を一緒に示すのが望ましい。
など。
また、以下の規格も参考になるので、合わせてご確認ください。
IEC62079(JIS C 0457)電気及び関連分野―取扱説明の作成―構成、内容及び表示方法